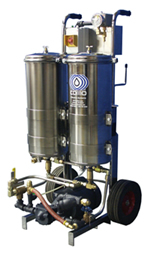
Problem: A plastic injection molding company was experiencing severe particulate and water contamination in their hydraulic oil. The contamination was causing multiple problems including:
- Sticky Valves
- Seal Leakage
- Component Part Failure
- Increased Downtime
- Increased Labor and Disposal Costs
With around 1400 gallons of oil, it would have cost them over $11,000 to change the oil at the time. Our customer wanted to both extend the life of the oil and protect their equipment.
Solution: They started filtering their oil through our Como Model 120/5 Portable Oil Filtration cart. After filtration, oil analysis reports show that the performance criteria specified by the client had been exceeded. An ISO 15/14/11 Cleanliness Code is now consistently achieved through filtration with our Model 120 and their oil is dry.
Filtration extended the hydraulic oil life to 3X its normal life so the Model 120/5 paid for itself within three months! This customer liked the results so much they bought a second Model 120!
Because of your separators and service, I was able to help one of my customers in a pinch and I have been able to grow my business from 3 employees to 26!”
-Gabe, Portland, OR
Case Studies - Quench Oil Filtration
Read our case studies to see how JDI, Inc.s equipment and services have solved a multitude of complex filtration issues.
Major Aviation Engine Manufacturer Case Study
We inspected each filtration system for proper operation and then gathered oil samples and had them tested at a certified lab for particles, % water and viscosity.
Case Studies - Heavy Equipment
Read our case studies to see how JDI, Inc.s equipment and services have solved a multitude of complex filtration issues.