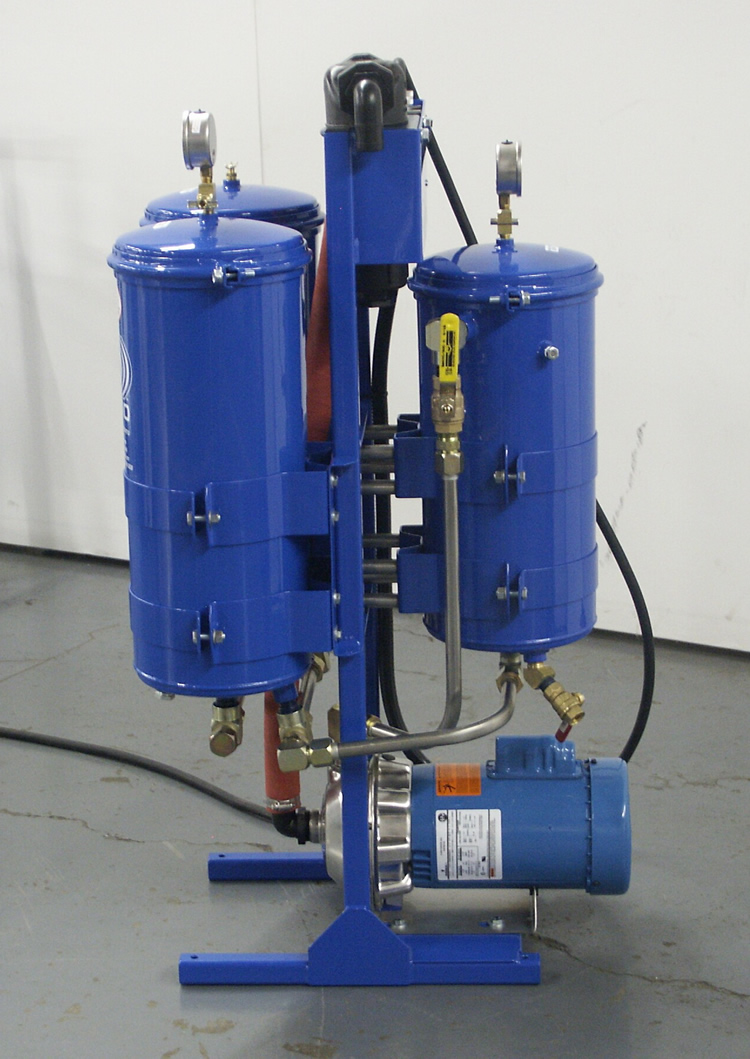
Quench oil systems typically face a number of operational issues including particulate contamination, water contamination and chemical alteration.
As metal is quenched in an oil bath, fines, including carbon particles and tiny bits of flash form in the quench oil. As these fines build up, localized differences in heat transfer occur in different parts of the bath. As a result of this inconsistent heat transfer, localized hardness can differ on the same part, or parts may even warp depending on size and shape. Additionally, parts can be stained with particulate after the quench process, requiring additional cleaning downstream.
Our turnkey filter systems are designed specifically for continuously filtering quench oils to reduce the effects of contamination. Let our quench oil experts help you incorporate a quench filtration system into your operation to maximize your company’s efficiency, quality and profitability. Call 1-800-453-8639 for more information.
Benefits include:
- Maintaining the oil's quench speed and cooling rates
- Reducing the chance of fire by maintaining a higher flash point
- Improving quench quality and reduce the number of rejected parts
- Extending the life of quench oils, reducing oil purchases.
Features include:
- Chrome Plated Filter Housings with Element Lifter - smaller units
- Hoist & socket assembly for element removal - larger units
- Positive Displacement Gear Pump
- High Temperature External Pressure Relief Valve
- 115 V 1PH motors for smaller units, 240/480V 3PH motors for larger units
- Motor Starter with thermal Overload Protection
- Pressure switch with high/low shut-off for unattended operation
- NEMA 4 enclosure with emergency stop and indicator lights
- On/Off Switch
- Pressure Gauge to Monitor Element Loading
- Inlet Wye Strainer
- Heavy Duty Powder-coated Frame with Heat Shield - smaller units
- Frame with fork channels for transporting - larger units
Quench Systems | For System Volumes, Gallons | Filter Housings | Bag Filter Housings | Pump, GPM Motor, HP | Pump Type | |
---|---|---|---|---|---|---|
![]() |
Model C-265/5QH | < 1000 | (2) C-1000 CP | 5 GPM 1 HP?? 115 V 1PH |
Hatrid | |
![]() |
Model C-465/10QH | > 1000 | (4) C-1000 CP | 10 GPM 2HP?? 115 V 1PH |
Hatrid | |
![]() |
Model 502 | Up to 5000 | (2) C-1200 PC | CB-850 | 15 - 20 GPM 2HP 240/480V 3PH |
Hatrid Iron Gear Pump with Buna Seals |
![]() |
Model 503 | Up to 7500 | (3) C-1200 PC | CB-850 | 20 - 30 GPM 3HP 240/480V 3PH |
Hatrid Iron Gear Pump with Buna Seals |
CASE STUDIES - QUENCH OIL FILTRATION
Please review our case study on a recent quench oil filtration system project. The problem was a machine tool manufacturer with an average weekly metal pass through of 30,000 lbs per week had been having trouble with oil contamination. This oil contamination resulted in non-uniform hardness, cracking and stained parts. The oil had to be disposed of frequently to improve the quality of the parts. Click Here to Review Our Solution
Why filter your quench oils?
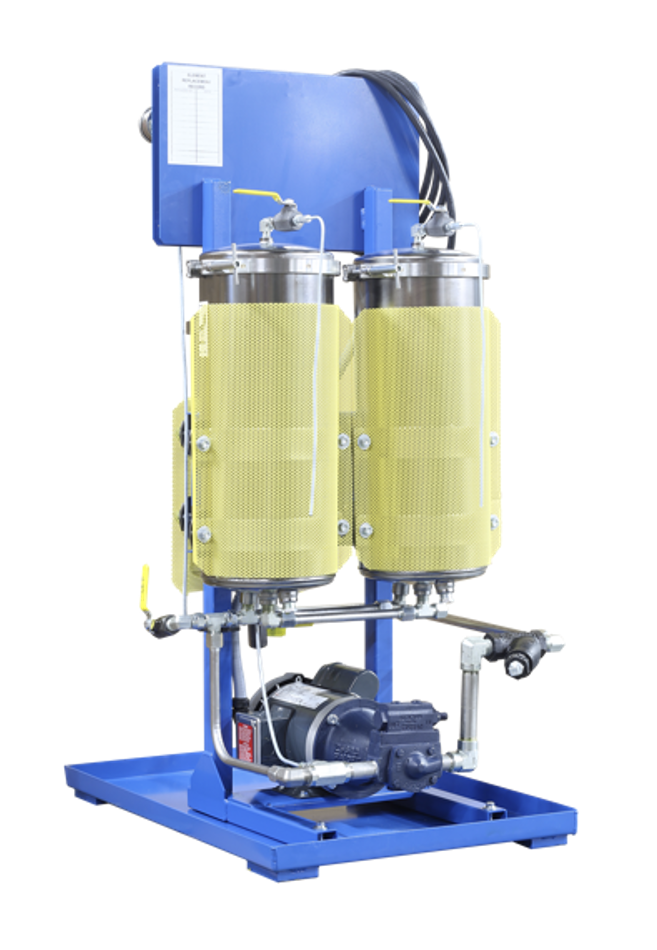
Operating and maintaining quench systems can be a complex undertaking. Common contaminants such as water, soot, salt, sludge (oxidation) and hydraulic oils affect the quenching performance of the oil. If contamination occurs, it is expensive to drain, dispose of, and replace the oil - not to mention the time required for this process to happen.
How does multi-pass continuous filtration help?
- Provide Even Heat Transfer across the Quench Bath - The heat transfer characteristics of the carbon, flash, and other fines in the quench oil are all quite different from the surrounding quench fluid. As these fines increase in population in the surrounding quench fluid, the heat transfer rate of the bath also changes. Filtration will assure the quench speed will be uniform across the quench bath.
- Reduce Thermal Cracking and Warping - Localized differences in heat transfer on the parts in the bath can cause inconsistent hardness on the same part, or even warping depending on size and shape of the part.
- Reduce Staining - Parts can be stained or contaminated with particulate after the quench process. Filtration will reduce staining and the need for a better (read-more expensive) processes downstream to clean the parts.
- Maintain Quench Speed - In a working quench system, there is no guarantee the quench speed will be uniform across the quench bath, as compared to virgin quench fluids. Quench filtration will remove contamination and help maintain the quench speeds and cooling rates of the quench oil.
- Improve Oil Quality & Reduce Liability - Additionally, filtration can greatly improve the quality of the heat-treating process, reduce the number of rejected parts, and save money by extending the life of quench oils.
- Reduce Liability - Most importantly, contamination in quench reduces the flash point of quench oils. A lower flash point makes flash fires a higher probability as hot metal is lowered into the quench oils. Filtering quench oils returns the flash point closer to the virgin flash temperatures, lowering the potential in your plant.
Additional product images of our Quench Oil Filtration Systems
